BGP128 Operation Manual 3.0
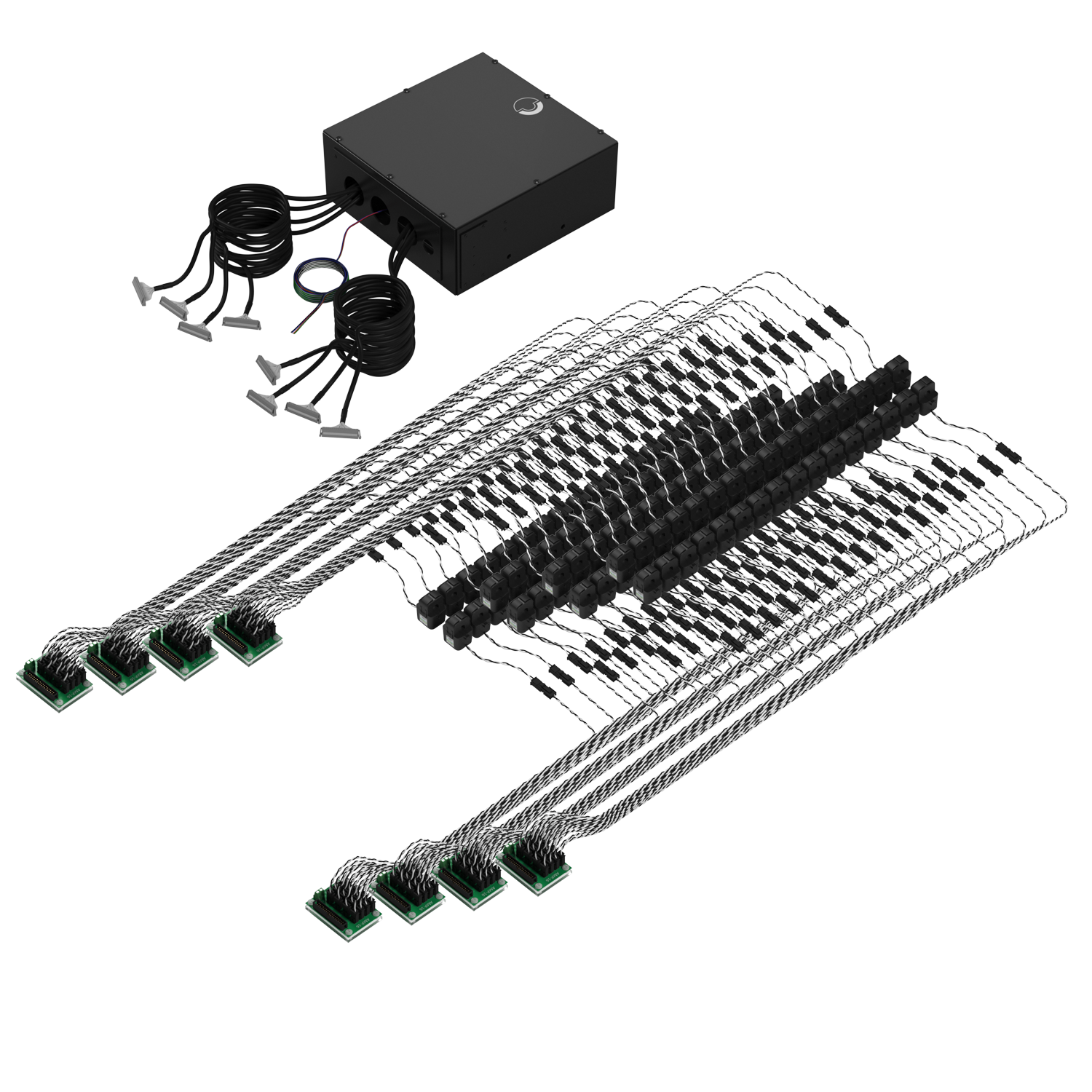
Overview
The Branch Circuit Monitor (BCM) is a power monitoring system designed for installation on power distribution panels. The BGP128 Model supports up to 128 breaker poles.
The system transmits the monitoring information via a wireless mesh network to one or more Packet Power Ethernet Gateway (“Gateway”) devices.
Hazards and Cautions
Read all instructions carefully prior to installation.
Always ensure power has been disconnected prior to doing any work.
The Branch Circuit Monitor (BCM) should be installed only by qualified technicians. Familiarity with and understanding of all terms used in this manual is assumed.
BCM should be deployed in conjunction with proper branch circuit protectors.
The user is responsible for ensuring that all work is performed in accordance with local electrical codes and regulations and using appropriate tools and materials.
BCM should only be connected to the type of power source indicated on the label.
The current transformer(s) used with the BCM must be appropriate to the amperage of the circuit(s) on which they will be used.
Only current transformers approved by Packet Power should be connected to the BCM. Using unapproved current transformers could result in inaccurate readings and damage to the BCM device.
Current transformers shall provide two means of isolation from hazardous voltages. When selecting a current transformer, the voltage and measurement category of the circuit to be measured must be considered to ensure that the current transformer is adequately insulated and rated. For 480V circuits, insulation shall be at least 600V rated. For 240V circuits, insulation shall be at least 300V rated.
Prior to installation, check to make sure the BCM has not been damaged.
Following installation in the final product, the connectors on the BCM must be fully enclosed and insulated from the external product enclosure in compliance with all relevant local electrical codes and regulations.
A safety connection to electrical ground / earth must be used.
Once installed on a conductor, current transformers must be connected to the BCM. Failure to do so creates an unsafe condition and will result in damage to the CT.
Follow basic safety precautions to reduce the risk of electrical shock and damage to equipment.
Store in a clean, dry location. Clean with a dry cloth.
Intended for indoor use only. do not install in a wet location.
Always use proper PPE when working in energized environments.
Packet Power LLC assumes no liability for user’s failure to comply with these safety guidelines. Please read this entire manual carefully before proceeding. |
---|
This symbol is used throughout this manual to indicate critical safety information. Failure to observe the information following this symbol may result in injury or death. |
CAUTION: This system and the area it is installed in may contain life threatening voltages. Qualified personnel must disconnect all high voltage wiring before using or servicing the BCM. Always use proper PPE when working in energized environments. |
3∿ The BCM will be pre-configured to support single-phase, split-phase or three-phase power as indicated on the product’s label. Only use the device with the indicated voltage service type. |
Do not apply or remove the current clamps from hazardous live conductors. |
Regulatory Information
Monitoring UnitsThis product has been tested to the following requirements: |
---|
CONFORMS TO UL/EC STD 61010-01, 3rd ed.IEC 61010-2-030 ed. 1.0, EN 61010-1:2010, CSA C22.2 NO. 61010-1 |
IEC 61010-2-032 - Edition 2 - Issue Date 2002/09/01, EN 61010-1:2001, IEC 61010-1, 3rd Edition. |
Council Directive 1999/05/EC - European Union (EU) Radio & Telecommunications Terminal Equipment Directive (R&TTE) ETSI EN 300 220-2 v2.4.1, ETSI EN 300 328 V1.7.1 and ETSI EN 301 489-1 and 301 489-3, Issued:2002/08/01 V1.4.1, EN61326-1, EN6100-3-2, EN6100-3-3, EN301 489-17, AS/NZS CISPR 11. |
IC RSS-210 Issue 8 Annex 8, RSS-GEN Issue 3. |
FCC CFR 47.15(C), 15.247(a) |
BCM AssemblyThis product has been tested to the following requirements: |
---|
UL508A Industrial Control Panel Class B Device Statement: This equipment has been tested and found to comply with the limits for a Class B digital device, pursuant to part 15 of the FCC Rules. These limits are designed to provide reasonable protection against harmful interference when the equipment is operated in a commercial environment. This equipment generates, uses, and can radiate radio frequency energy and, if not installed and used in accordance with the instruction manual, may cause harmful interference to radio communications. Section 15.19 of the FCC Rules: This device complies with part 15 of the FCC Rules. Operation is subject to the following two conditions: (1) This device may not cause harmful interference, and (2) this device must accept any interference received, including interference that may cause undesired operation. |
BCM Disassemby |
---|
The BCM contains components that may fall under local electronics disposal guidelines. Please adhere to local requirements. |
No lead is used in the BCM. |
Supported Voltage Service Types
The BCM comes pre-wired for use with one of the following service types:
Voltage | Configuration | Wires |
---|---|---|
208/120V 415V/240V 480V/277V | Three Phase WYE | 3 Phases + N + Ground |
208V | Three Phase Delta | 3 Phases + Ground |
240V/120V | Split Phase | 2 Phases + N + Ground |
Ensure that the type of voltage service that is present in your panel matches the type indicated on the label of the BCM. The BCM cannot be used on 480V panels if no Neutral line is present. The BCM also cannot be installed if the Neutral line is on a separate panel which exceeds the supported voltage such as a 600V/347V Panel. The BCM is powered directly from the voltage source it is monitoring.
Current Transformers
The BCM is pre-configured for use with either 15A, 30A or 50A 333mV output split-core Current Transformers provided by Packet Power. CTs can be safely used on circuits up to 130% of their nominal rating (for example the 50A CT can be used on circuits up to 63A). The unit may also be configured with up to six 100A to 400A CTs to monitor up to two infeed circuits per BCM.
Use of the CTs on circuits with greater than maximum load will result in degraded accuracy and damage to the CTs
CTs should not be removed from conductors while under load. Once installed on a conductor that has load present, the CT must be connected to the BCM. Failure to do so will create a safety hazard and result in damage to the CT.
The CTs are attached to the BCM via a wire harness that terminates in a CT Interconnect Board. The number of CT Interconnect Boards varies by model. The CT Interconnect Boards are typically mounted inside the panel and are connected to the BCM using the provided CT Interconnect Cables (shielded ribbon cables).
Communication
The BCM utilizes Packet Power’s advanced zero-configuration wireless mesh networking technology which automatically connects the BCM to an Ethernet Gateway when energized. Each Gateway can support multiple BCMs; additional Gateways can be added for capacity or redundancy.
The BCM must be able to establish a wireless connection either directly to a Gateway or to another Packet Power wireless device.
Data can be accessed from the Gateway in one of two ways:
Third Party Device Data Acquisition - Third party monitoring systems can access data from a Gateway via SNMP, Modbus TCP/IP, Ethernet/IP, MTConnect, BACnet/IP and MQTT protocols.
Cloud Based Data Acquisition - Data can be simultaneously exported to the Packet Power EMX monitoring portal (local or cloud based).
Equipment Parts Lists
The BGP128 consists of a NEMA 1 monitoring enclosure, up to 8 CT interconnect boards with wire harnesses for attaching CTs, and the CTs themselves.
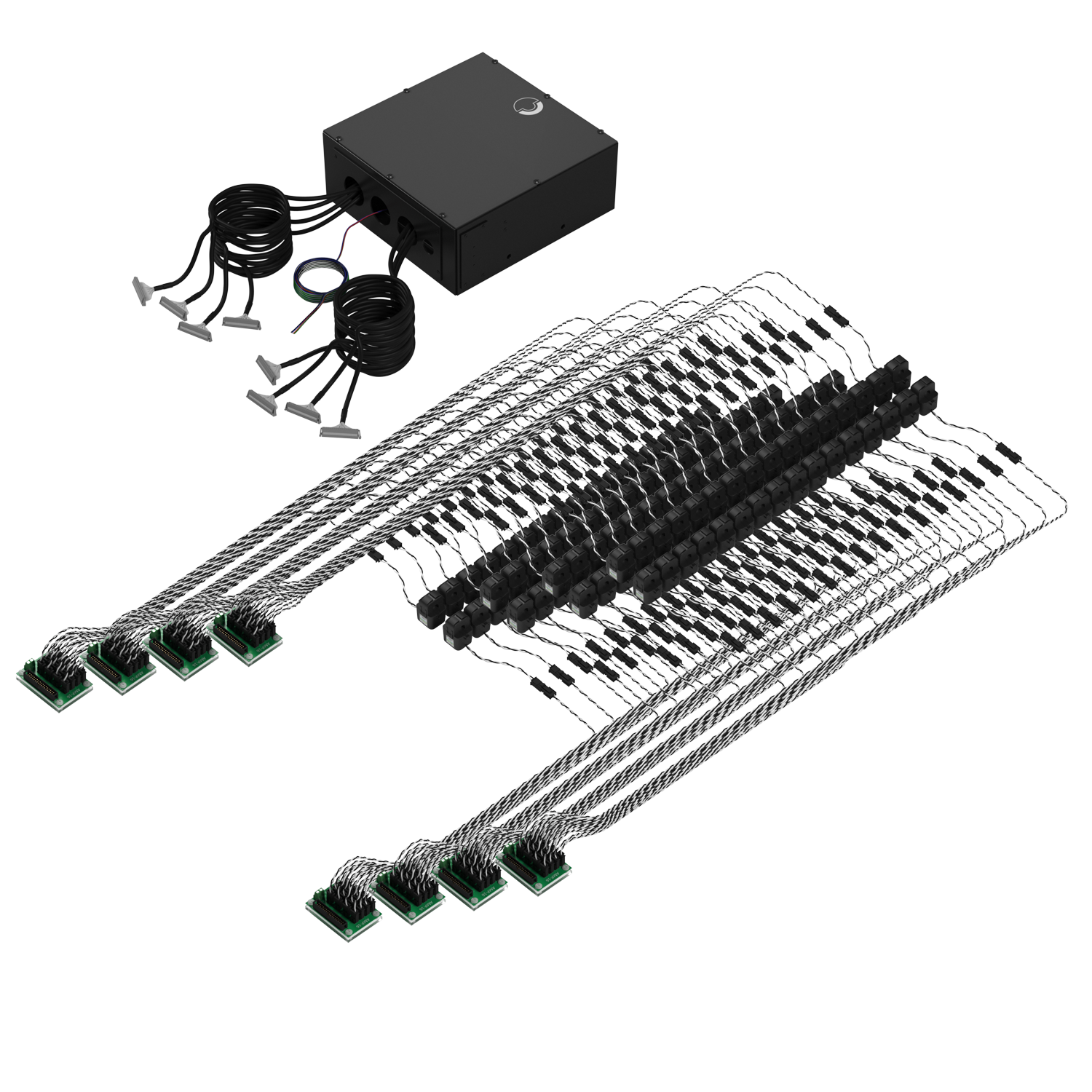
BGP128 COMPONENTS | |
---|---|
Device: | Up to 16 wireless monitors in an 18 GA steel enclosure with plastic front |
Mounting Brackets: | Two optional 18 GA steel brackets |
Voltage Leads: | 1B AWG 600V colored wire connected to a |
CT Interconnect Cables: | Up to eight shielded 300V cords in any mix of 1m, 2m, 3m, 5m, or 10m lengths; terminate in a 34-pin connector that fastens to the CT interconnect board |
CT Interconnect Boards: | Up to eight 72 x 53 x 6.3mm (2.8 x 2.1 x 0.2 in) acrylic-backed boards with VHB adhesive tape for mounting. |
Branch Circuit CT Harness: | Wire Harnesses |
Current Transformers | Up to 128 CTs; |
Of these items, the following can be replaced in the field by qualified personnel:
Enclosure cover
Metering combs (located inside [A])
Fused voltage harness
CT interconnect board
Split core CTs
Installation
Important
Installation should be conducted by a qualified professional according to local electrical codes.
Protective equipment should be used when handling a current transducer (CT) on a live conductor.
Do not make adjustments to the BCM’s internal wiring.
If you believe the BCM, CTs, interconnect boards or leads have been damaged, do not attempt to repair or use them. All components are built to spec by Packet Power and are not intended for alteration in the field.
Please review the complete list of safety instructions in the Hazards sections of this document.
Installation Steps
Mount the BCM enclosure using mounting brackets provided.
Run the voltage lead(s) to the PDU(s) and connect them to L1, L2, L3, N and earth.
Run the CT Interconnect Cables inside the PDU(s).
Mount the CT Interconnect Boards inside the PDU(s).
Attach the connector at the end of the CT Interconnect Cable to the CT Interconnect Board header.
Route each CT harness inside the panel and secure as desired.
Connect each CT to the appropriate conductor and then connect the CT tail to the corresponding CT wire harness lead
The BCM does not need to be configured prior to use. Once power is supplied, the BCM will automatically begin to transmit data. Thoroughly review the details for each step prior to installation. Contact Packet Power support with questions.
Mounting
The BCM should be mounted as close as possible to the panel(s) being monitored. Use the steel mounting brackets provided.
Mounting locations
The following are common locations for mounting your BCM.
PDU Top: Wire Exit: Back Opening
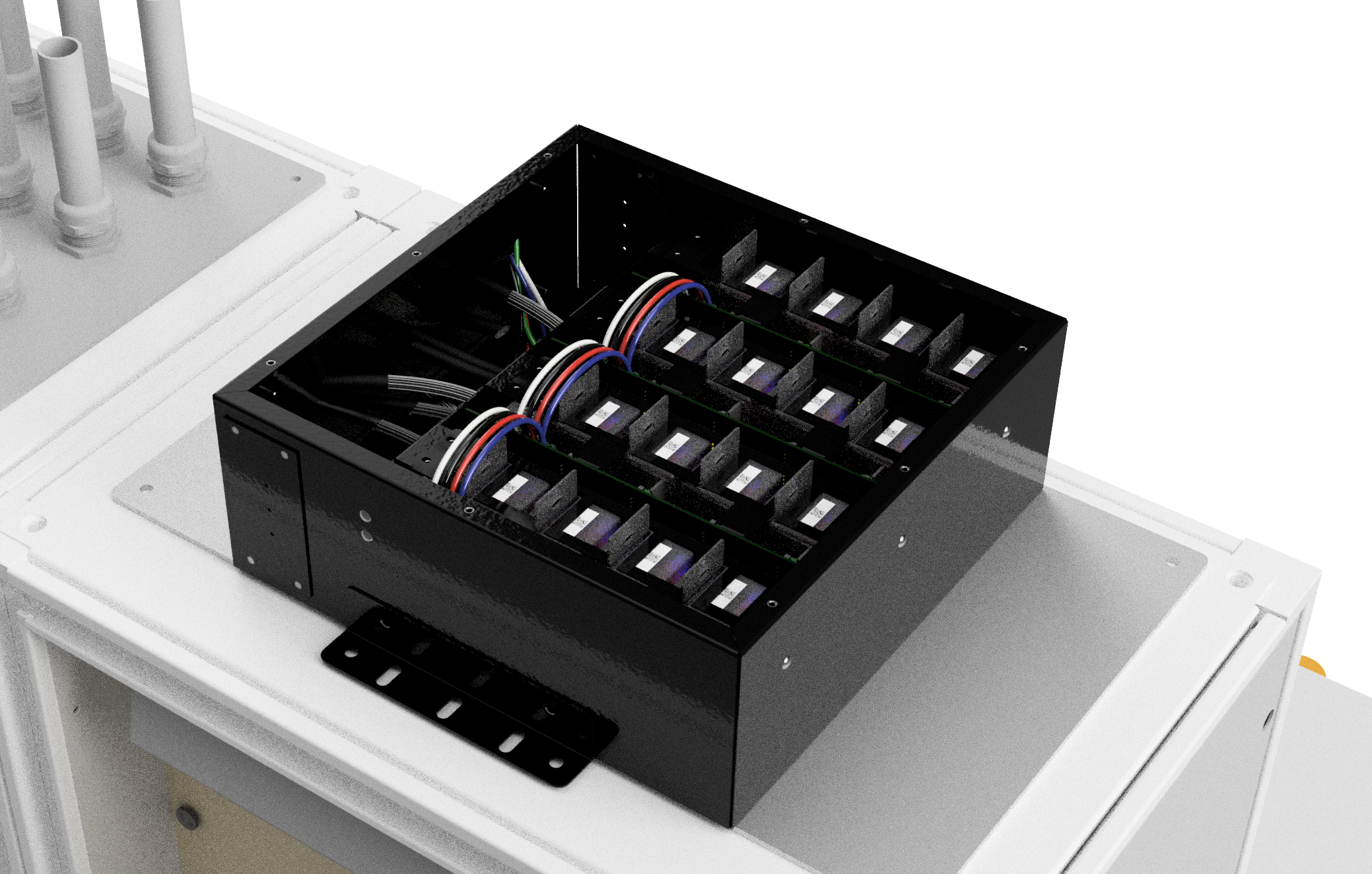
Wall Mount: Wire Exit: Bottom Opening
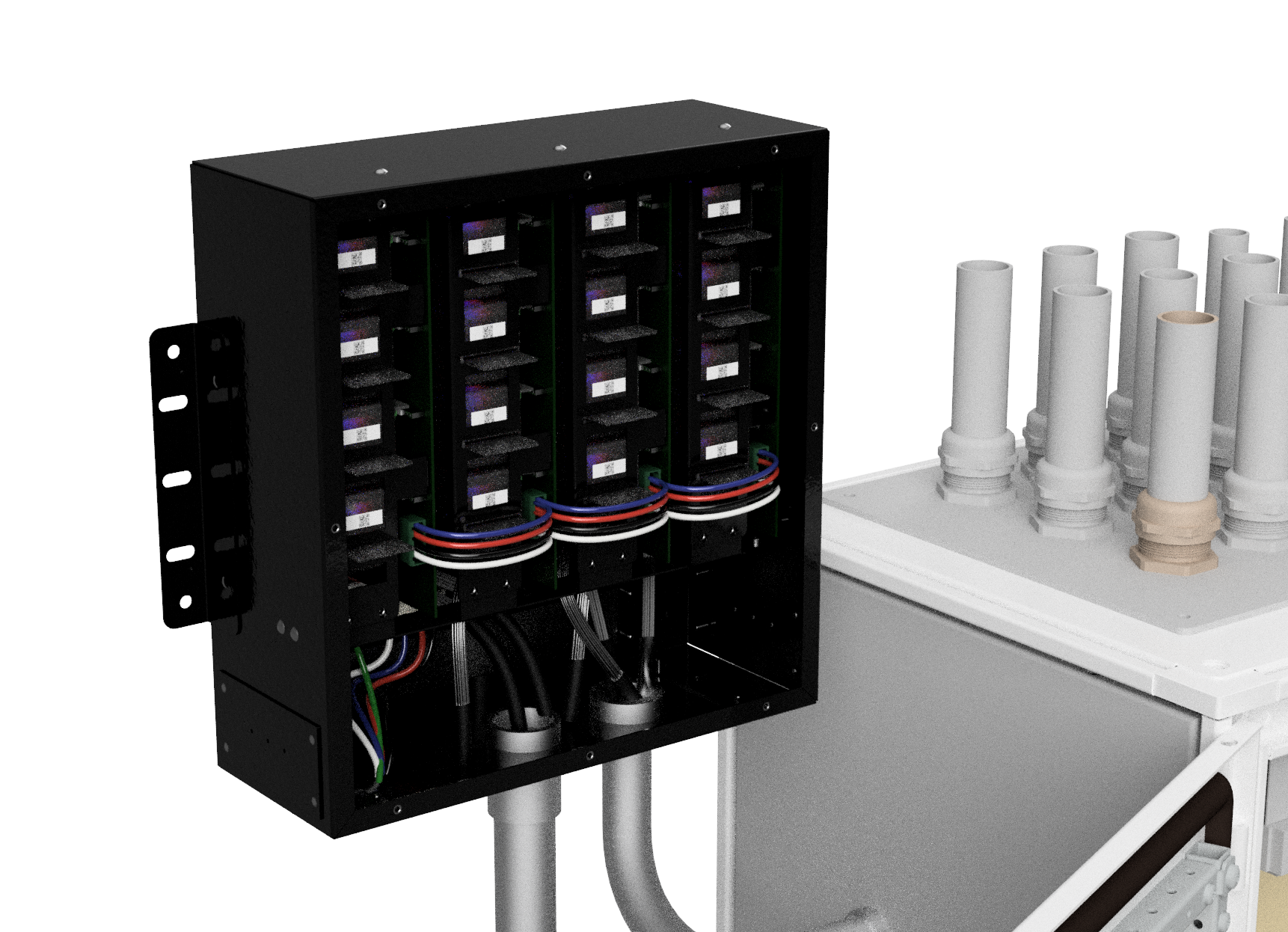
PDU TOP: Wire Exit: Bottom Opening
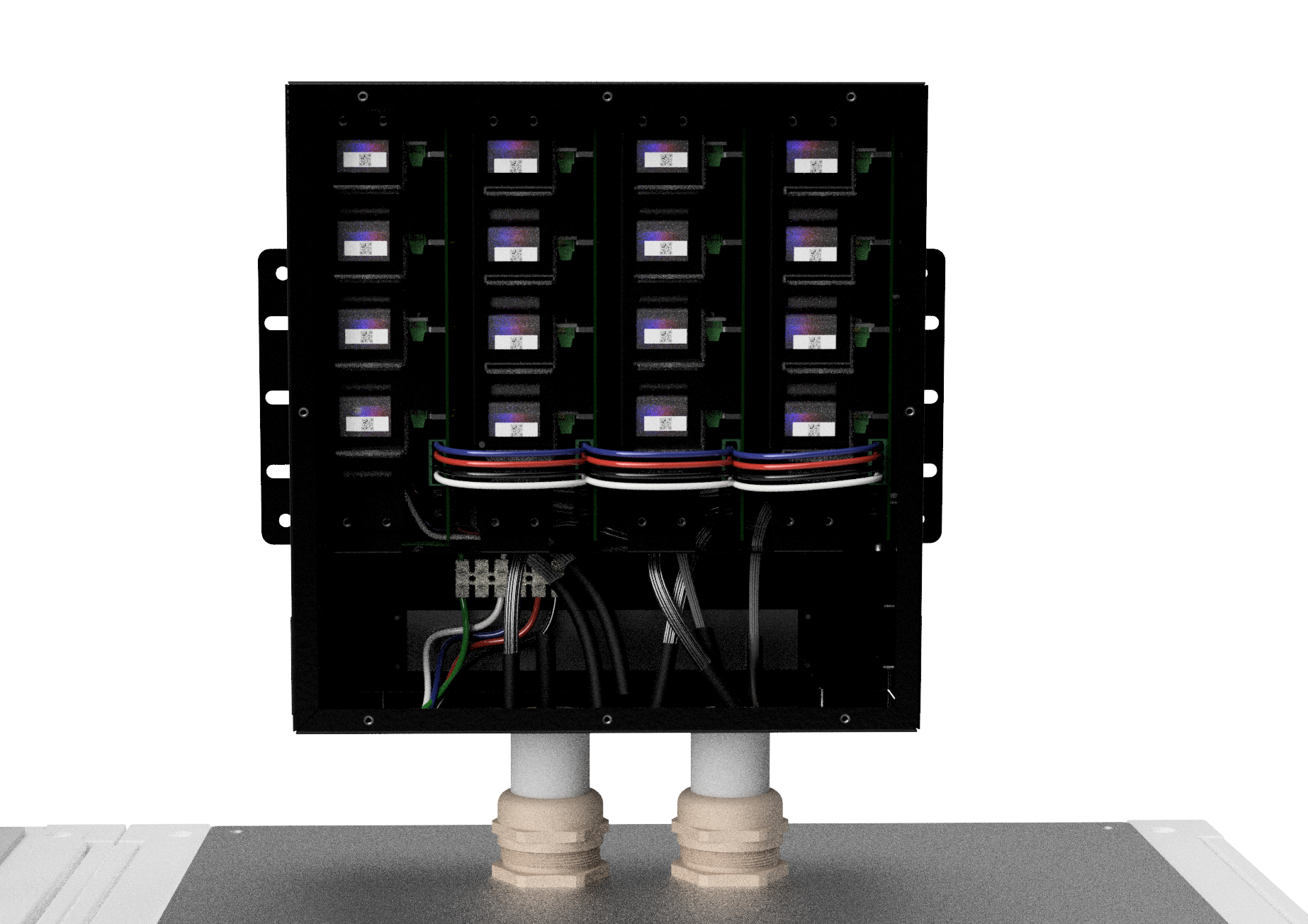
PDU Top: Wire Exit: Left or Right Side Opening
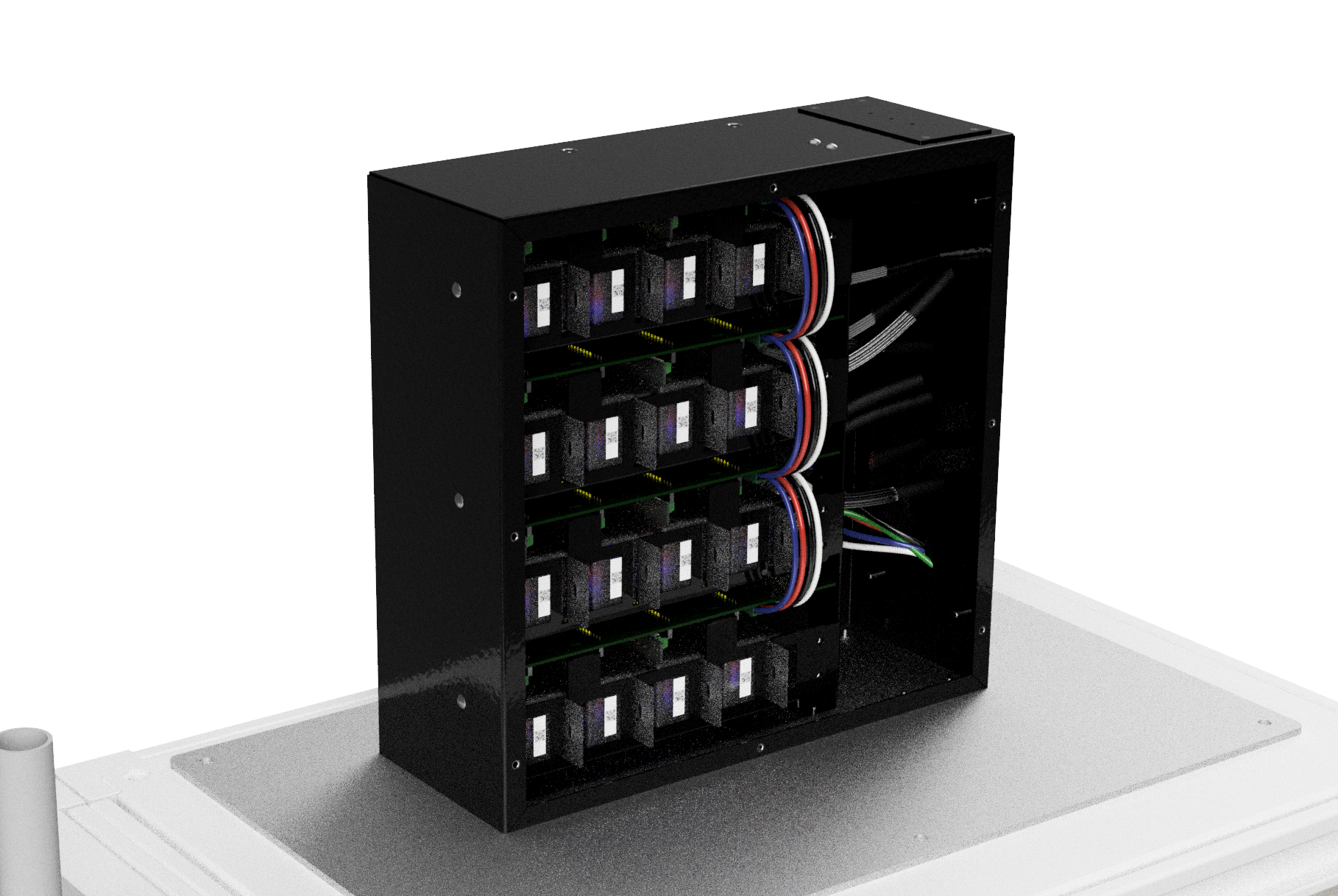
UNDER RAISED FLOOR: Wire Exit: Left, Right, or Bottom exit.
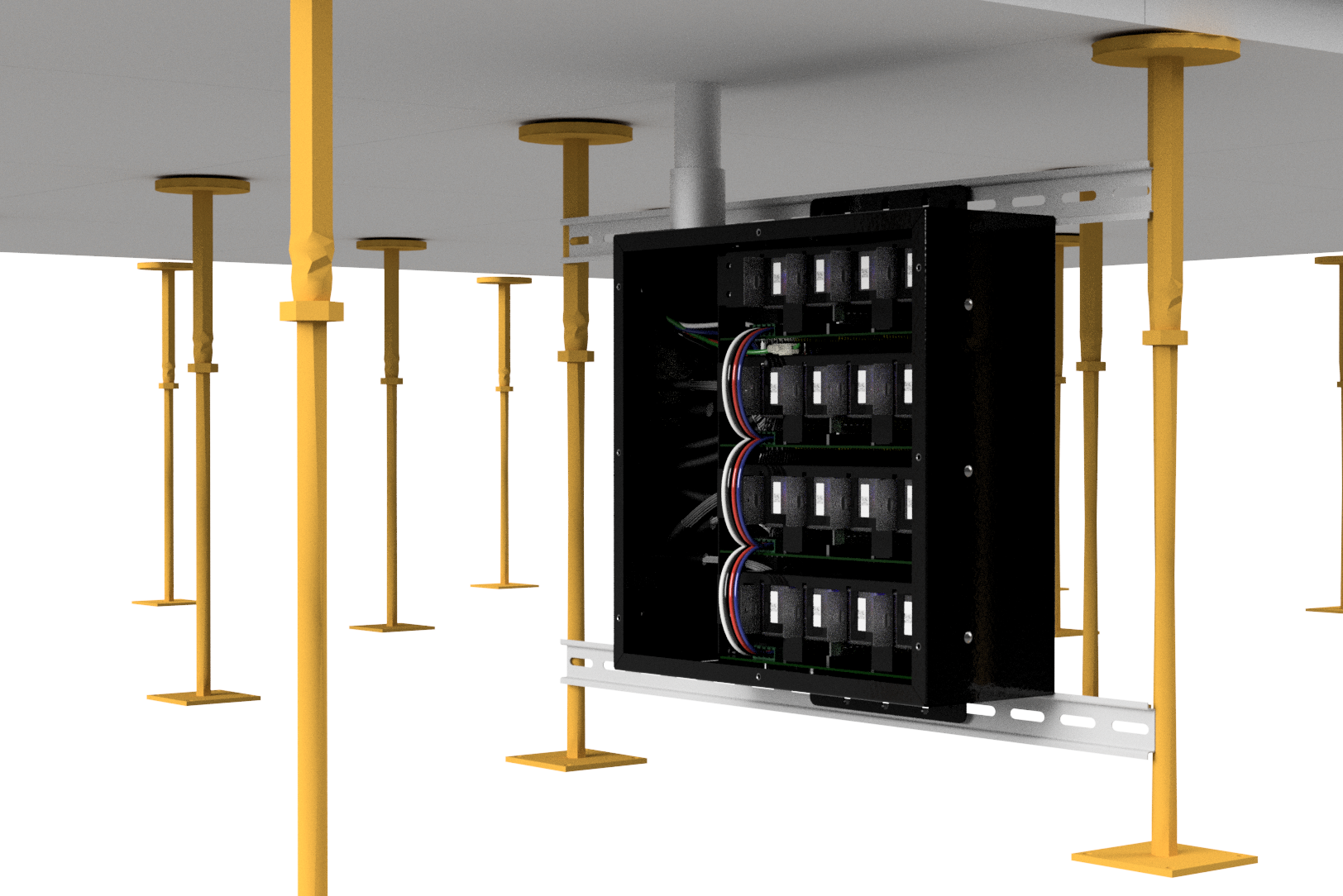
BCM enclosure dimensions
Without mounting brackets | With mounting brackets |
---|---|
310 x 302 x 115 mm (12.2 x 11.9 x 4.5 in) | 310 x 352 x 115 mm (12.2 x 13.9 x 4.5 in) |
Wire exits
The BCM has openings for wire exits in the back and on each side as well as a conduit plate on the bottom end of the unit. This allows it to be mounted in a variety of positions relative to the panel(s) being monitored.
Bottom Conduit plate | Back Opening | Left Side Opening | Right Side Opening |
---|---|---|---|
3 x 1.75” (44 mm ) knockout 1 x 0.875” (22 mm) knockout | 8.75 x 2.00” (222 x 51 mm) | 1.875 x 3.75” (48 x 95 mm) | 1.875 x 3.75” (48 x 95 mm) |
Voltage Connection
A three-pole breaker should be used to provide over-current protection and a means of disconnecting power from the BCM. If a three-pole breaker is not used, you must ensure suitable over-current protection is provided.
The BCM unit comes pre-wired. Each device is configured to work with one of the supported voltage types. Unless otherwise specified, the unit has inline fuses on each voltage phase. The wire count and color mix will vary based on the voltage service type (see table on following page).
Voltage leads
18 AWG 600V wires which are connected to a 6-position terminal block inside the enclosure are provided for use in routing power to the device.
Voltage lead lengths are sized to specification. They may include a voltage disconnect near the BCM that is used to avoid placing strain on the connection to the terminal block during shipping and installation.
5x20 mm 5A inline fuses are included on L1, L2 and L3 unless otherwise specified.
An optional second voltage source can be included on panels with dual feeds. If a second voltage lead is included, the voltage leads will be labeled accordingly.
Wire connections
The BCM uses different wire colors depending on service type and region. Run the voltage leads to the voltage source and connect them to L1, L2, L3, N and earth. Reference wire connections by service type on the following page.
Verify that the wires are connected to the proper phases for your type of voltage service.
No changes should need to be made to any wiring within the BCM device itself.
Grounding
Failure to properly ground the unit could result in a dangerous or fatal electrocution.
The BCM enclosure must be properly connected to earth. A ground wire is provided for this purpose.
Once power is supplied the BCM will automatically begin to transmit data.
208/120V WYE
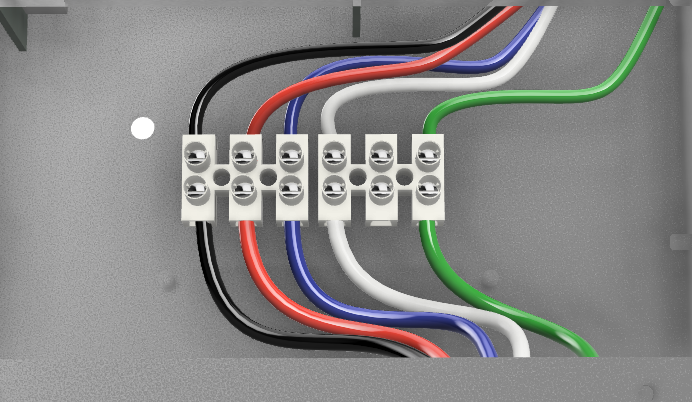
208/120V WYE
208V Delta
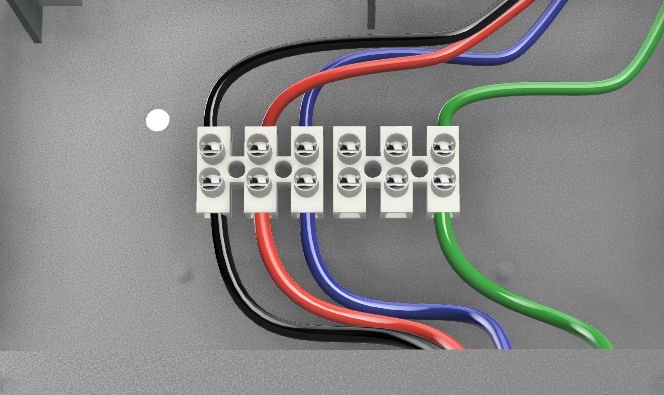
208V Delta
240/120V Split Phase
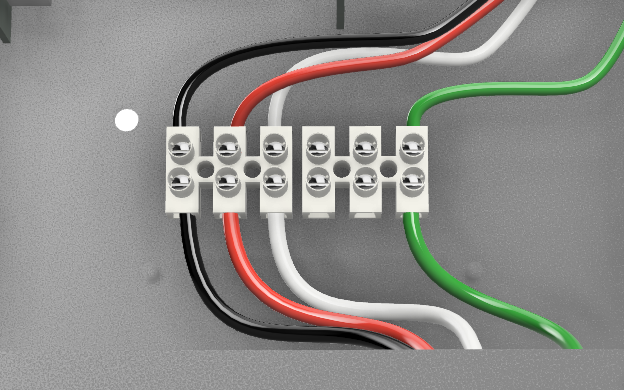
240/120V Split Phase
415/240V WYE
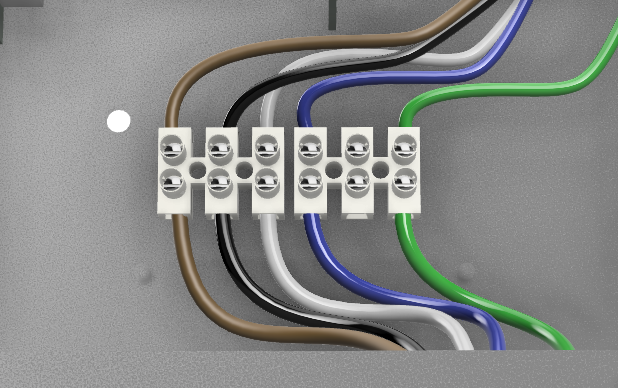
415/240V WYE
480/277V WYE
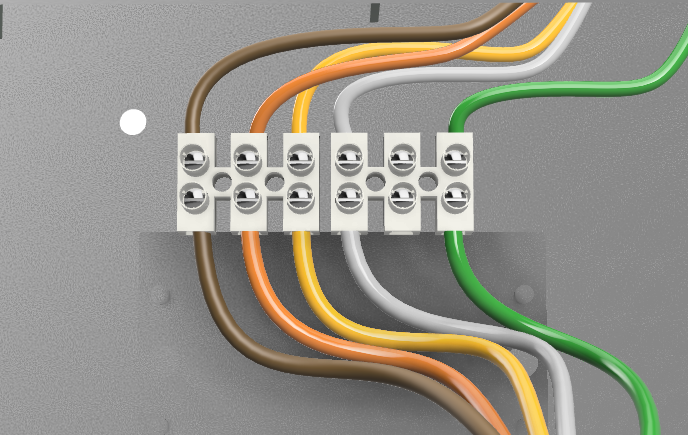
480/277V WYE
Voltage Tap Connection Methods
Dedicated circuit breakers
Utilizing a small existing circuit breaker on a panelboard is among the most common methods of accessing voltage.
Spare terminals
Some PDUs, RPPs and switchgear contain small auxiliary terminal blocks that can be used to source voltage for the meter.
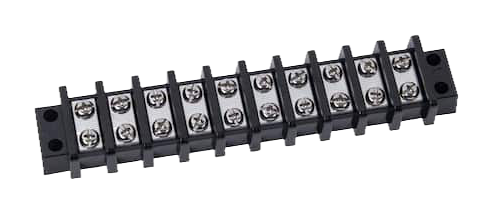
Insulation displacement connectors (IDCs)
IDCs pierce the insulation on an existing conductor and provide a means for safely connecting a second "tap" line that can be used to source the voltage. These connectors are available in many sizes and are specified according to the primary and tap conductors. Most are UL listed and code compliant but may not be accepted in all jurisdictions.
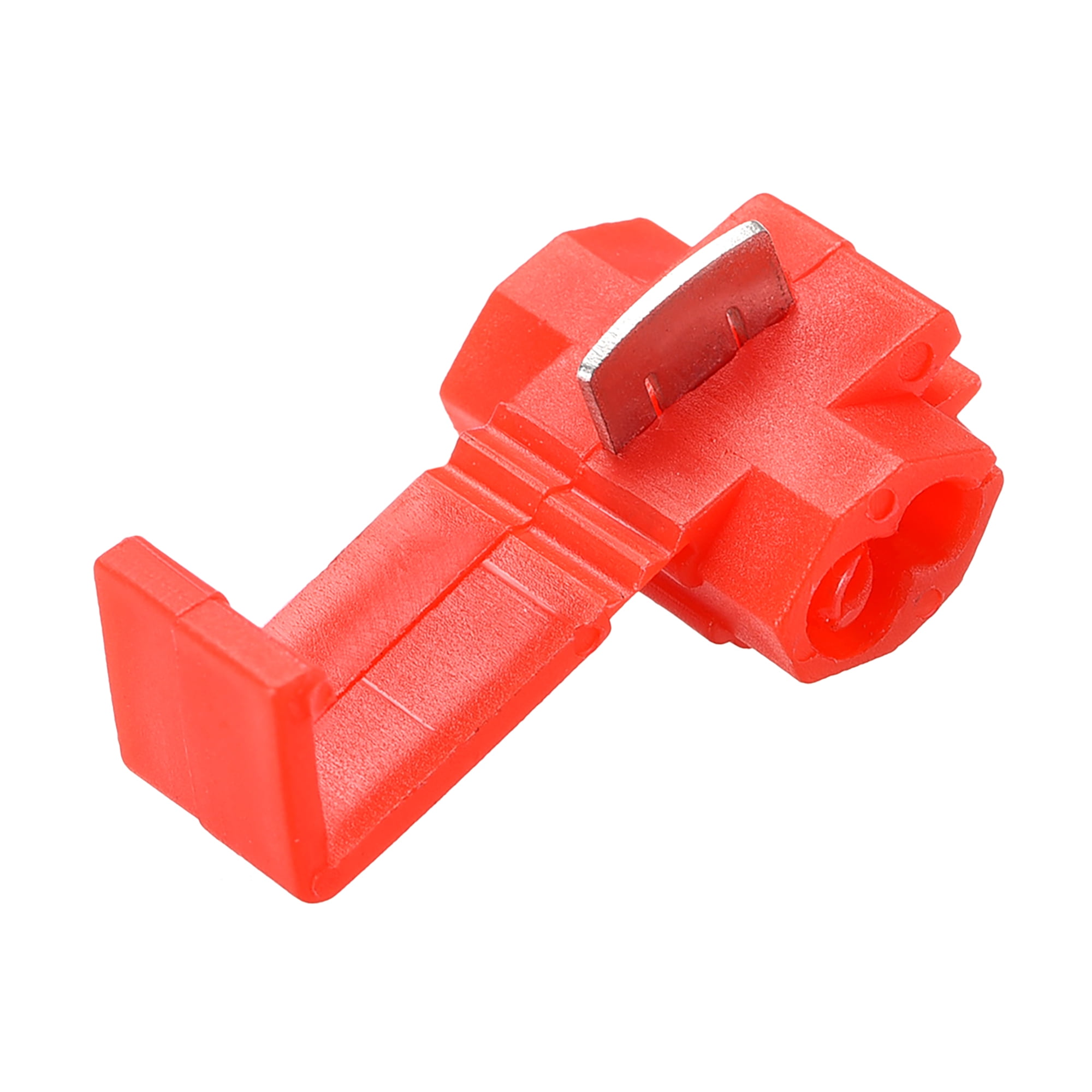
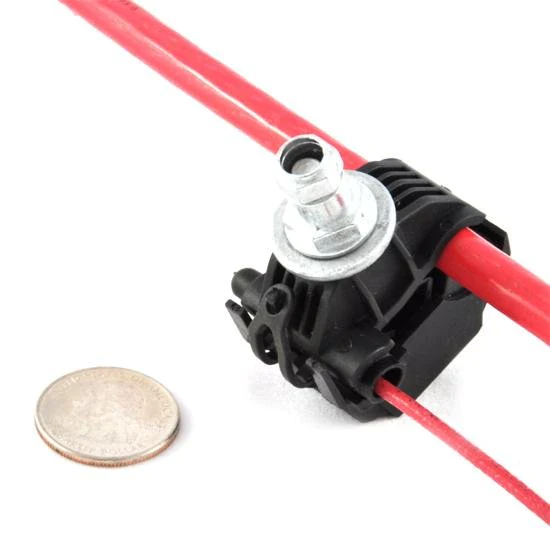
Tapping the busbar
Electricians drill and tap the busbar and attach the conductor directly to the busbar using a ring terminal.
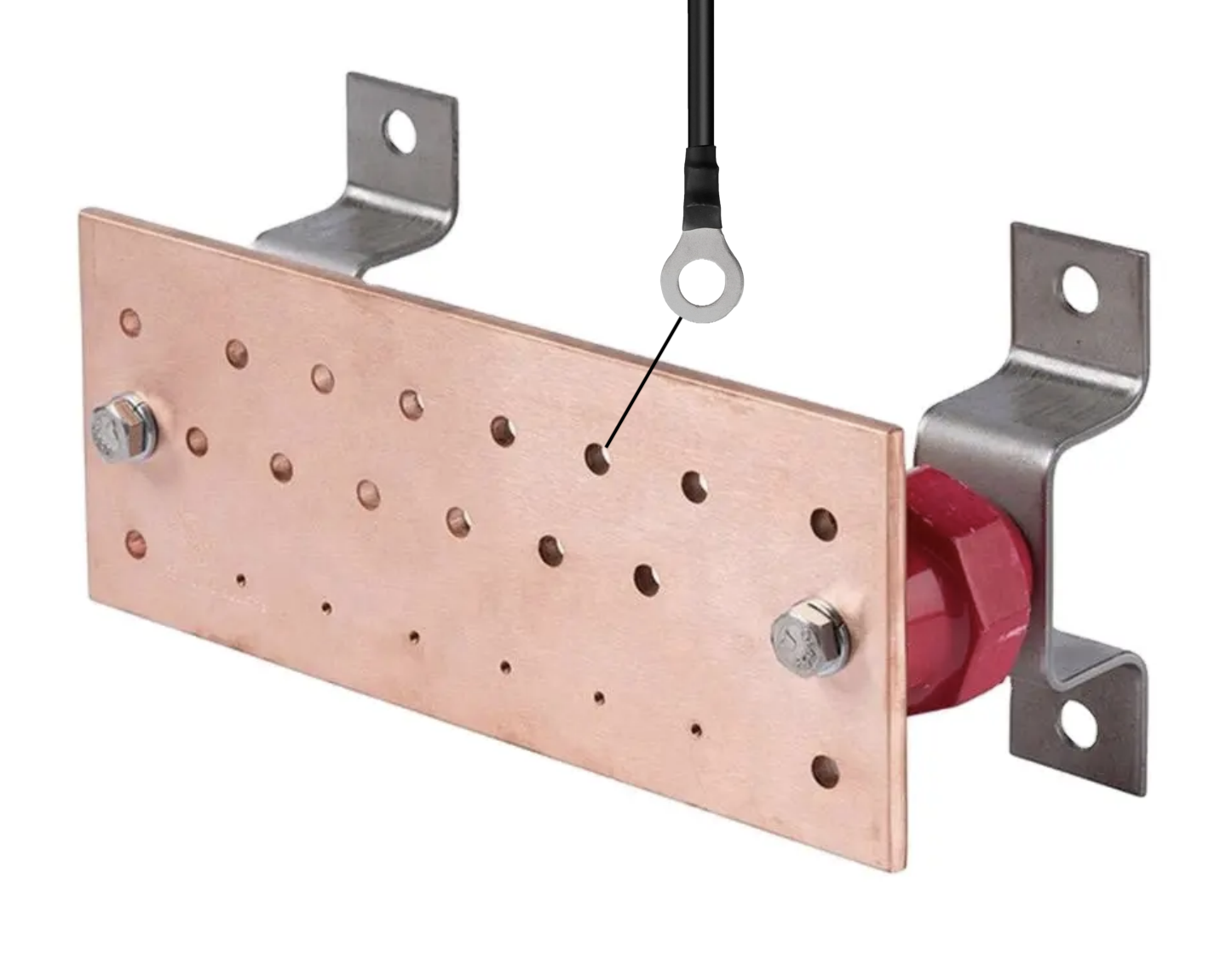
Busbar taps
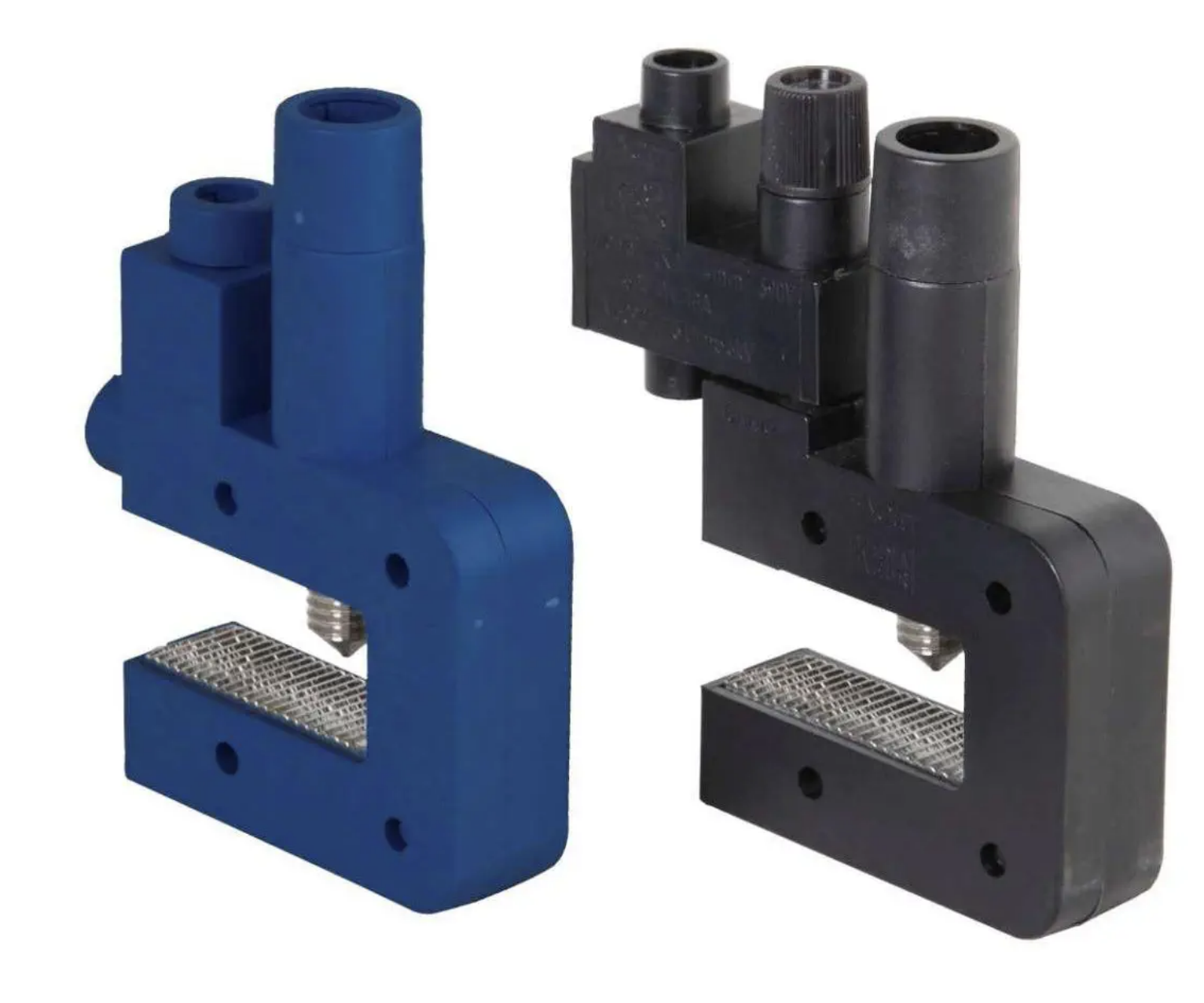
Busbar taps clamp directly to an existing busbar and allow for a secondary voltage tap. This approach is more common in Europe and not typically used in North America. Busbar taps can be expensive but are essential in some applications.
Double lugging
The practice of double lugging entails sharing the lug or terminal of the conductor with the voltage sensing wire. This is done when the primary conductor is much larger than the voltage tap wire. Ideally this is done where there are large compression lugs securing the primary conductor. Double lugging may not be approved in all jurisdictions.
Cable splitter via wire nut or twin wire ferrule
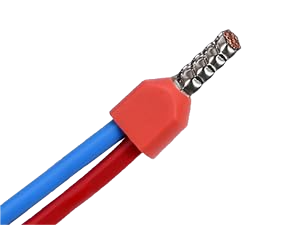
When the primary and tap conductors are close in size, the best practice is to use a single conductor entering the terminal of the voltage source. This single conductor can then be branched into two sources after it leaves the terminal using a code compliant method such as a wire nut or twin wire ferrule.
This is a brief summary of the most common ways to tap into a voltage source. Please note the acquisition method most suitable for your facility is subject to your regional electrical codes and the judgement of a qualified electrician familiar with the job at hand.
CT Interconnect Cables and Boards
Each CT Interconnect Board will be labeled with a number, panel and/or circuit identifier (e.g., 1A, 1B, 2A, etc.) that will match a corresponding label on the fastener end of one of the black CT Interconnect Cables.
Run CT Interconnect Cables inside the PDU
CT Interconnect Cables connect the BCM to the CT Interconnect Boards. Run the shielded ribbon CT Interconnect Cables from the BCM to the inside of the PDU(s).
Mount CT Interconnect Boards
The green CT Interconnect Board is fastened to a 72 x 53 x 6.3 mm acrylic base with VHB adhesive tape on the back of the base.
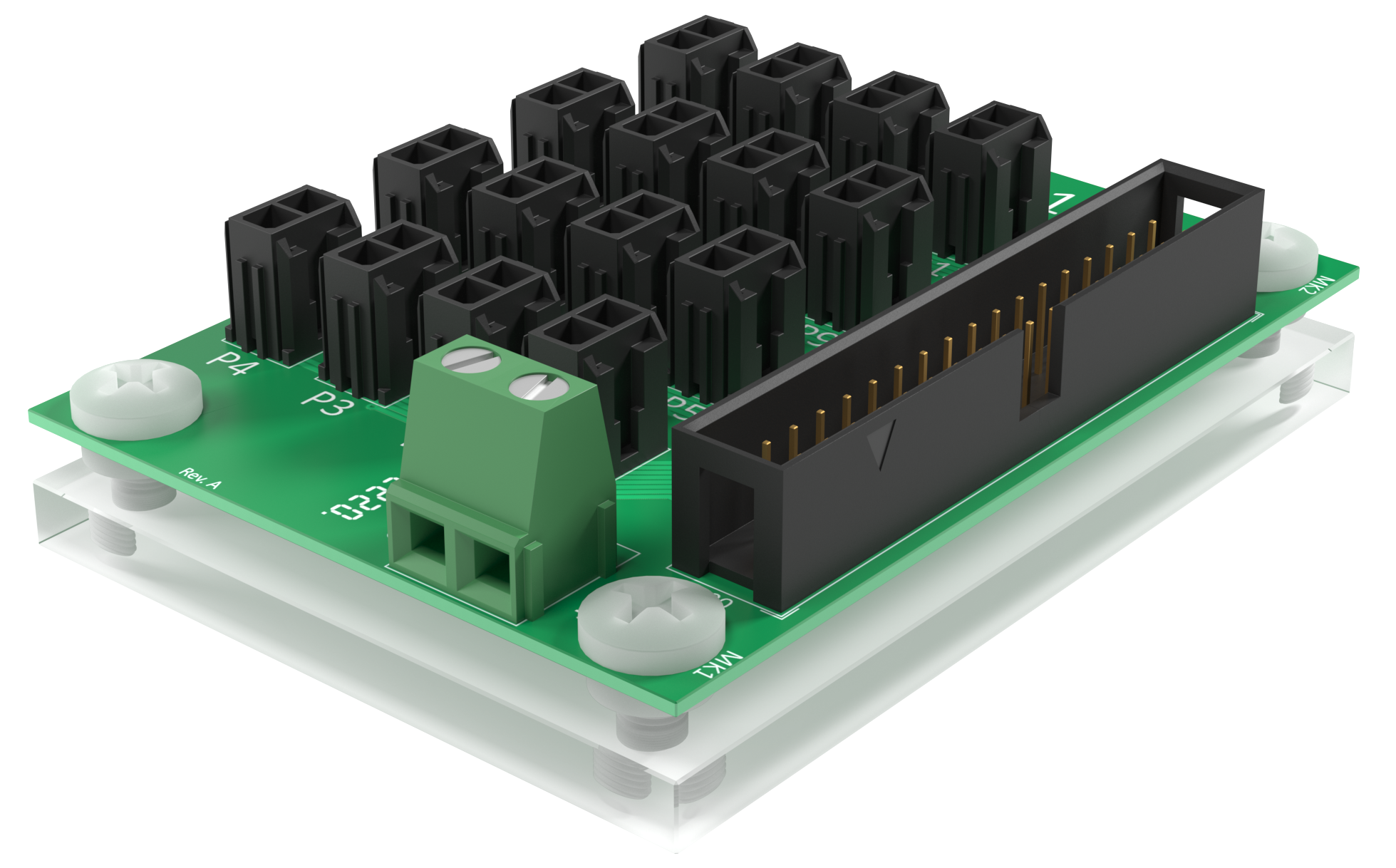
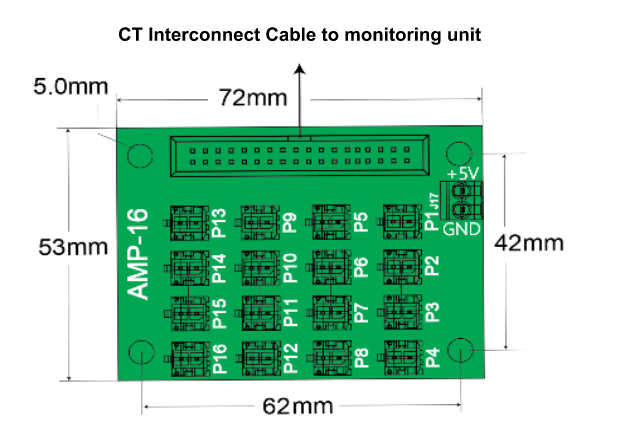
Clean the area thoroughly, then mount the CT Interconnect Boards inside the PDU using the VHB adhesive tape (or mount using 5/32” screws). Be sure to orient the CT Interconnect Board so the black connector header faces away from the panel.
Attach Interconnect Cable to Interconnect Board
Attach the connector at the end of the CT Interconnect Cable to the corresponding CT Interconnect Board header. The interconnect cables and boards are labeled:
Comb 1 | 1A, 1B |
Comb 2 | 2A, 2B |
Comb 3 | 3A, 3B |
Comb 4 | 4A, 4B |
CT Wire Harnesses
Branch circuit CTs are connected to the CT Interconnect Boards via a wire harness consisting of up to 16 leads per harness. Packet Power offers multiple harness configurations and will match the best fit to the layout of your panels. Here are some wire harness examples.
Secure CT wire harness inside panel
Run the CT wire harness inside the panel and secure it as desired. The wire harness will be attached to the CT Interconnect Board. Each CT lead will have a label (the labels vary by panel type).
CTs
Each BCM model supports the following number of branch circuit or branch circuit + optional infeed circuit CTs.
Branch circuit CTs only | Branch circuit + Infeed circuit CTs |
---|---|
60 to 128 | Up to 122 + 6 -or- Up to 125 + 3 |
Branch Circuit CTs
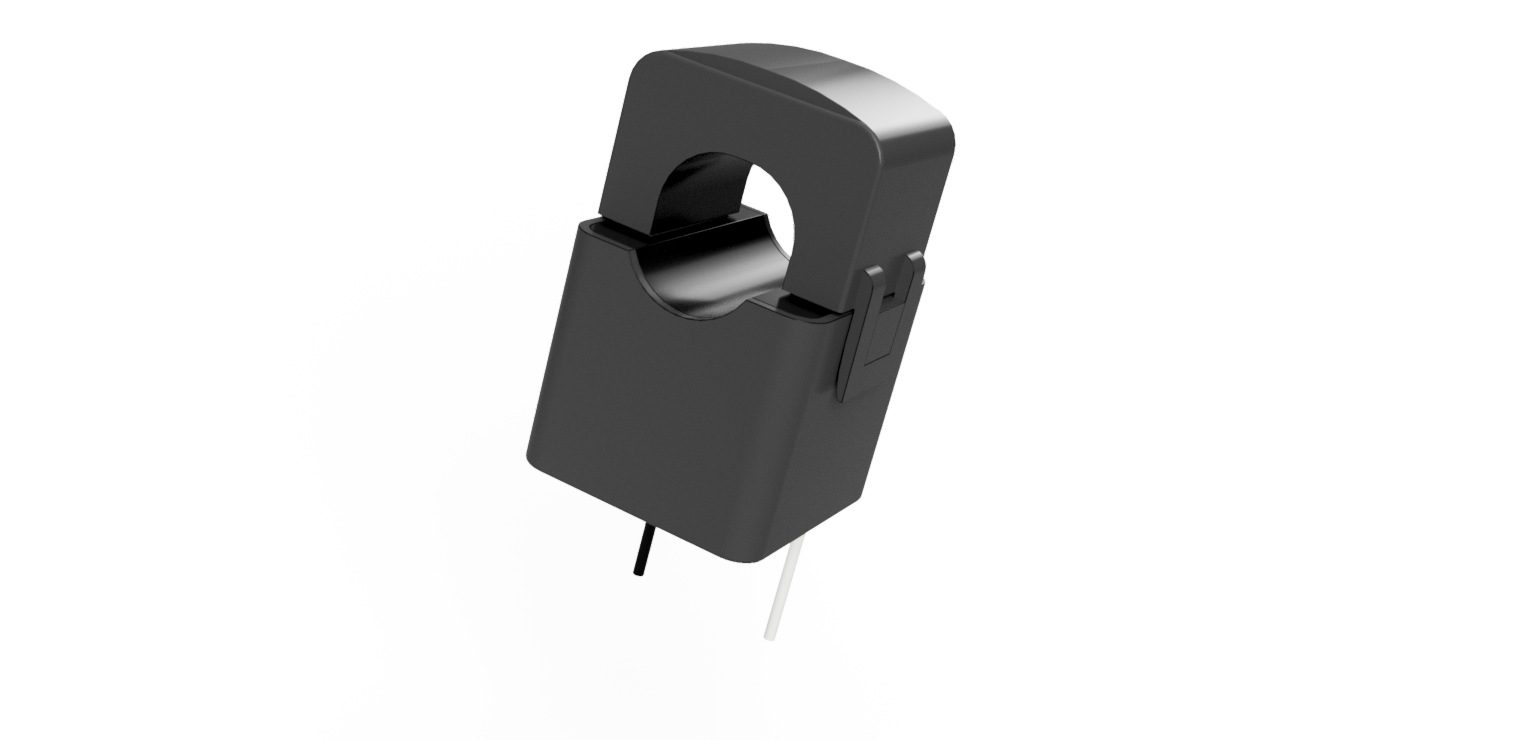
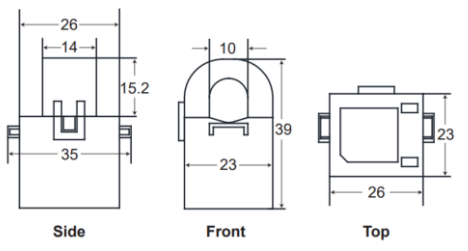
Branch Circuit CT Specifications | |
---|---|
CT quantity | Up to 96 |
CT type | Split core |
Accuracy | +/- 1.0% |
Inside diameter | 10 mm |
Outside dimensions (H x W x D) | 39 x 23 x 26 mm (1.5 x 0.9 x 1.0 in) |
Rated amperage | 15A, 30A or 50A |
CT tail | 100 mm (4 in) to quick disconnect |
CT tail wire | 24 AWG, 600V twisted pair |
Optional Infeed Circuit CTs
Up to 6 CTs may be specified for use on the panel infeed circuits rather than on branch circuits. Applicable CT leads will be labeled for use with the infeed CTs. The infeed circuit CTs are typically 100 to 400 amps and will have an inside diameter of 24, 36 or 50 mm depending on the model selected.
Infeed Circuit CT Specifications | |
---|---|
CT quantity | Up to 6 |
CT type | Split core |
Accuracy | +/- 1.0% |
Inside diameter | 24, 36 or 50 mm; varies by model |
Outside dimensions (H x W x D) | Varies by amperage |
Rated amperage | 100A to 400A |
CT tail length | 500 mm (20 in) to quick disconnect |
CT lead length | 0.5 to 5 m |
CT tail and lead wire | 24 AWG, 600V twisted pair |
Connecting CTs to conductors
Disconnect power to the BCM if possible.
If it is not possible to disconnect power, always treat CT leads as though they carry line voltages. Work on live panels must only be performed by qualified personnel.
Open the split core CT by opening the latch on the side of the CT (Figure 1).
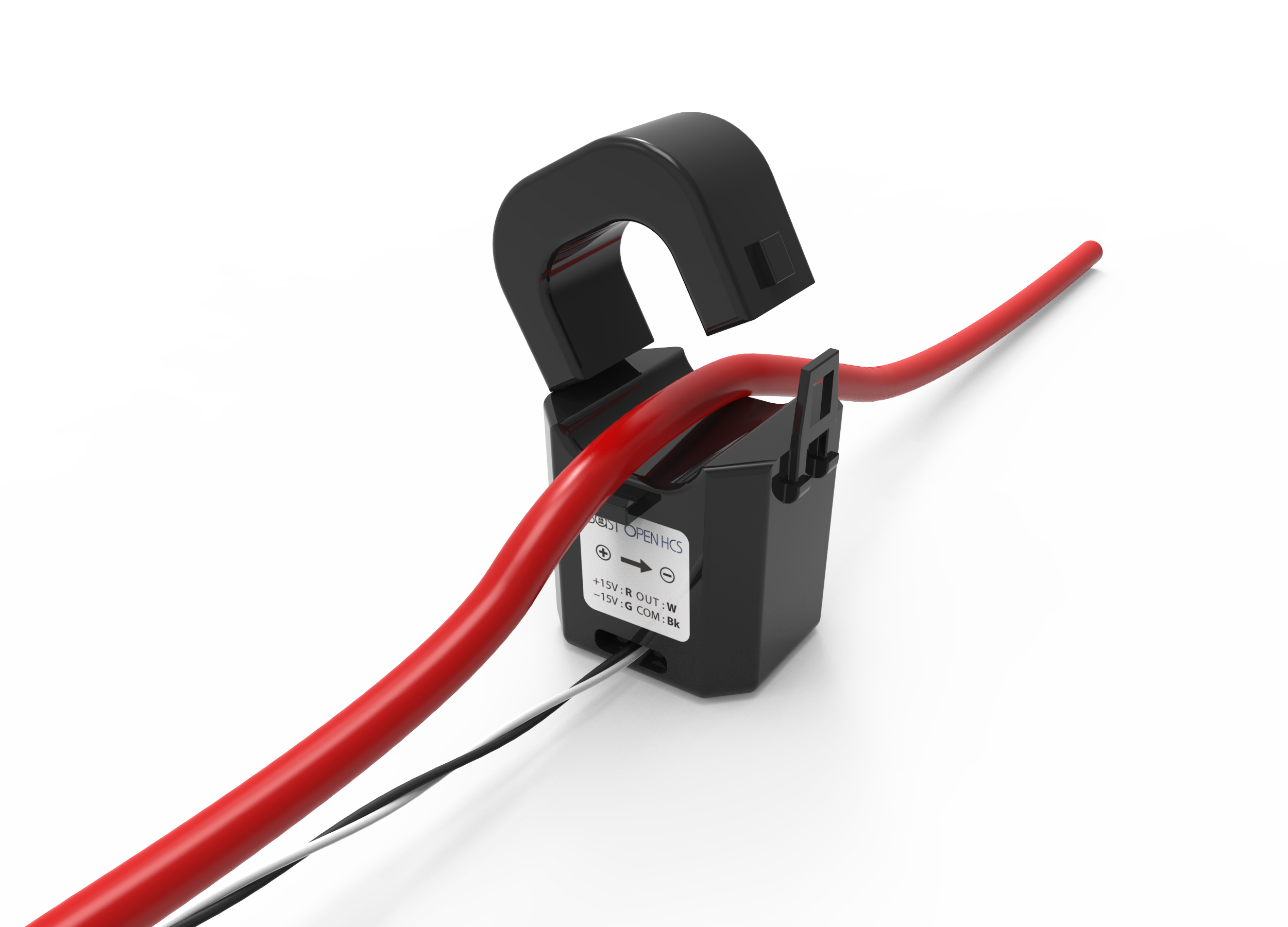
Figure 1
Position the CT on the conductor such that the CT lead faces toward the load and away from the source.
Close the CT and ensure the latch has clicked into place.
Connecting CT tails to CT leads
CT leads on the wire harness will be labeled with odd/even circuit numbers. Connect the branch circuit CT tail to the corresponding CT wire harness lead using the quick connectors. The power monitor automatically detects the correct phase once load is present.
Infeed circuit CT leads will be labeled CT1, CT2, CT3, etc. Connect the infeed circuit CT tail to the appropriate CT lead attached to the CT Interconnect Board.
The BCM uses CTs that produce an output of 333 mV.
Operations
Normal operation is characterized by the regular flow of monitoring data. This is typically verified on a continual basis via the site’s monitoring application. Please consult the monitoring application’s documentation for how to achieve this using your application.
/configuring gateway
/uploading panel definitions
/validating readings through panel definitions (gateway and EMX)
/how to extract data via modbus/snmp/mqtt.
/using the indexed channels (how they can get the indexed channels.
Start Up
The BCM ships fully pre-configured. Once power is supplied, the system will automatically connect to any Gateway that is within range and set to the same radio zone. For information on setting up an Ethernet Gateway See: https://dox.packetpower.com/support/current/ethernet-gateway-quickstart
To prevent damage to the BCM, ensure power is disconnected whenever abnormal or extreme power conditions may exist such as during infrastructure commissioning
The BGP128 contains up to 16 component power meters.
Each meter has LEDs that glow when powered on. The cover of the BCM is translucent, and it is possible to verify that all component meters are powered up by looking closely through the cover and verifying that the lights on all units are flashing in a consistent manner.
Each BCM has a unique 16-digit ID number that can be found on a label located on the outside of the unit in the top left corner. Each component meter also has an individual 16-digit ID number. Once the meter makes a wireless connection to a Gateway, the readings from that meter can be accessed via the Gateway’s console.
instructions for using the gateway web console can be found on dox.packetpower.com
Packet Power provides documentation that is unique to each BCM and associates each CT to its component meter. See Appendix for sample. This documentation is required in order to access readings using protocols such as SNMP or Modbus. Customers using Packet Power’s EMX application will be provided panel maps to load into EMX.
At initial start-up, it is highly recommended to validate correct operations by placing a known load on each circuit and verifying that the load is correctly reflected by the system, first at the Gateway console to validate the physical connection, and then in the monitoring application to validate the mapping logic.
Shutdown
No special preparation is required prior to shutdown. Using a customer-provided disconnect such as a 3-pole breaker, simply shut off power to the BCM. Note that this disables power to the monitoring unit only.
The conductors on which the CTs are installed will still have live load and must be treated accordingly, and the panel itself will still have live voltage and present a risk of electrocution.
Maintenance & Troubleshooting
Scheduled Maintenance
The BCM requires no periodic maintenance or calibration and there are no scheduled maintenance events. Customers are encouraged to keep firmware current by applying updates once a year or whenever a critical firmware release is issued.
Firmware updates can be arranged via Packet Power support and are available for all devices under warranty. This includes the original manufacturer’s warranty or the optional extended service warranty purchased after the manufacturer’s warranty ends.
Add or Replace a CT
Disconnect power to the BCM if possible.
If it is not possible to disconnect power, always treat CT leads as though they carry line voltages. Work on live panels must only be performed by qualified personnel.
Disconnect the CT to be replaced using the quick disconnect attached to the CT tail.
Open the CT by opening the latch on the side of the CT (Figure 1) and remove from the conductor.
Position the new CT on the conductor such that the CT lead faces toward the load and away from the source (Figure 2).
Comb Replacement
If one or more power meters are not responding, Packet Power can provide a new comb that can be replaced onsite by qualified personnel. This avoids the need to replace the entire monitoring device.
Before beginning work, ensure power has been disconnected to the BCM. Failure to do so could result in severe or fatal electrical shock.
You’ll need to provide Packet Power with the following information to facilitate a comb replacement.
Information needed | Where to find the information |
---|---|
16-digit ID number of the BCM | Small square label on the top left corner on the outside of the enclosure; label has Packet Power logo, QR code and 16-digit ID number |
16-digit ID number of the component meter(s) that is no longer working | 16-digit number from the small label on each component meter |
ID number of comb(s) that need to be replaced | 6-digit serial number from the larger label at the end of each comb |
Radio zone used on the BCM | Check the Ethernet Gateway’s radio zone setting (only necessary if you have modified the radio zone) |
Comb positions
Comb 1 | Meters C1-4 to C1-1 |
Comb 2 | Meters C2-4 to C2-1 |
Comb 3 | Meters C3-4 to C3-1 |
Comb 4 | Meters C4-4 to C4-1 |
Note that not all combs / meters are present in all configurations (for example some BGP128 models may only have 3 combs and some combs may only have 1, 2 or 3 meters).
Removing a comb
Ensure that power is off to the BCM.
Remove the BCM cover.
Unplug the green power connector from the circuit board on the comb that is to be replaced. If you are replacing comb 1, it is easier to also remove the power connector from comb 2; similarly for combs 3 & 4 as well as combs 5 & 6.
Remove the four #6 bolts on the comb to be replaced. Be careful not to drop them in the BCM device.
Lift up top side of comb.
Feed ribbon cable to pull comb out. If there is not enough ribbon cable to allow the ribbon cable connectors to be removed and re-connected, carefully cut the strain relief ties on the ribbon cables to provide more cable length.
Unplug the ribbon connectors making careful note of which ribbon connector goes into which connection point on the comb. It is a good idea to label the ribbon cables accordingly.
Please save the entire comb assembly to ship back to Packet Power for technical analysis.
Installing a replacement comb
Ensure Packet Power provides an updated panel schedule that incorporates the ID numbers of the component meters used in the replacement comb.
Plug the ribbon connectors into the replacement comb ensuring that the ribbon cables are connected to the proper connector; if they are mixed up, improper readings will result.
Tuck the ribbon cable out of the way while inserting the comb back into position.
Fasten the comb using the #6 bolts.
Re-insert the green power harness connector(s).
If needed, reapply strain relief on the wire exit side of the BCM to ensure there is no direct pressure on the ribbon cables.
Replace the BCM cover. Do not overtighten the screws.
Return power to the unit and verify that lights can be seen on all of the component meters in the replacement comb and the lights on all meters are flashing in a similar pattern.
If you are using panel schedules on your Gateways:
Upload the new panel schedule to the master Gateway.
Disable the existing panel schedule.
Enable the updated panel schedule and view the panel to ensure readings are flowing.
Delete the old panel schedule.
Troubleshooting
If the BCM does not light up once power is supplied:
Ensure access to power:
Check that the customer-supplied breaker protecting the circuit providing power to the BCM is closed and that the supplied voltage source leads have been connected to the proper phases See:
Check the quick disconnect
A quick disconnect may be present on the voltage leads near the supply side of the terminal block in the BGP unit. Separate it and reconnect it, ensuring there is a clean connection.
Check the inline fuses
Remove the BCM cover and locate the terminal block that connects to the voltage source wires. Follow the wire harness on the side of the terminal block that feeds into the BCM to locate the inline fuse holders. Open each fuse holder and inspect for blown fuses. Replace with 5x20mm glass 5A/250V fuses. Replace the cover and reconnect power.
Verify voltage presence.
If no power is flowing, use a multimeter to verify that voltage is present for each phase at these locations.
Where the BCM’s voltage leads connect to the customer-supplied protective breaker.
On the supply side of the voltage terminal block inside the BCM.
On the meter side of the voltage terminal block inside the BCM.
On each phase of the green terminal block connectors in the wire harness that distribute power within the BCM.
Contact Packet Power support with the results.
If a subset of the monitoring readings are missing:
Verify that all monitoring modules are active by looking through the cover of the BCM to see that all units are lit up and blinking in a similar pattern. If not, contact Packet Power support.
If all units are lit up, check to see that all units are reporting via the wireless mesh to a Gateway. Note that the LEDs on a meter that cannot join a mesh will flash using a different pattern than those that are communicating. If this is occurring, note the location of the missing meter (ideally, take a short video of the unit) and contact Packet Power support.
If you are using a panel map to translate pole-level readings into circuit-level readings and not all readings are present, ensure that:
The panel map is loaded and active on your master gateway.
Peering is enabled on the master gateway.
The IP address for all peer gateways has been entered on the master gateway.
If V readings are present but A and W are missing:
If only one reading is missing, follow the process listed in the Maintenance section of this document to remove the associated CT and re-install it on the conductor. Disconnect the CT from the CT harness and reconnect it, ensuring a clean connection.
If a number of readings are missing, ensure the CT Interconnect Cable is securely connected to the associated CT Interconnect Board.
If the BCM powers on but no units are able establish communications with a Gateway:
Contact Packet Power support.
Ensure gateway is not fully enclosed in metal as this can restrict wireless communication
If you receive Negative Power (W) or Energy Readings (kWh)
Negative readings are caused by CTs being placed backwards on the conductor. Locate the corresponding CT(s) and flip 180 degrees.
If you are unable to access the panel after it has been energized, please contact Packet Power for other options.
If you are unable to receive data via SNMP or Modbus TCP/IP
Please review the corresponding documentation via the following links. If issues still persist, please contact support@packetpower.com for further assistance.
Modbus TCP/IP: Modbus TCP/IP
SNMP: SNMP Data Interface
EMX: Power Readings
Inaccurate data (high or low readings, zero value, etc)
If you have discovered that pole level readings do not correlate with a local readout (digital display, amp clamp, etc) please contact Packet Power at support@packetpower.com for review of your Panel Definition file.
Emergency Measures
Contact Packet Power support at 1-877-560-8770 or support@packetpower.com.